Residential Wall With R13 and 5 Continuous

The building industry loves its standards. Even more, the industry loves a standard it can quantify as a number, which is easy to understand and compare. However, when we embrace these standards, we need to make sure we are understanding each number correctly. I find R-value is one standard that is often misunderstood. R-value simply describes a material's ability to resist heat flow—the higher the number, the better the R-value. With performance modeling and testing techniques, we have the ability to calculate the heat flow through any one isolated material. In the case of an entire building, however, we never use just one material. We build assemblies, and these assemblies typically have multiple pieces, each with its own insulating properties.
As builders and building designers, our goal, at its simplest level, is to create an indoor environment that is, by design, different from the outside environment. For most climates, this requires us to accommodate a difference (delta) in temperature, which in some cases can be extreme. The industry's answer to mitigating this delta is insulation. Typically, the higher the delta, the more insulation. The measurement of the insulation is R-value. While this numerical standard has served the industry well, it's only part of the equation.

Evaluating Whole Walls
As an industry, we tend to equate the R-value of a building's exterior walls with the R-value of the insulation in the assembly. For example, a 2x4, 16-inch-on-center wood-framed wall that is using an R-15 batt is labeled as an R-15 wall. This is where the standard and reality begin to part ways. Yes, the center of the stud cavity is R-15. The wall, however, is not just a stud cavity; it's a series of sticks that we call studs, plates, headers, sills, and so on. These sticks don't have the same resistance to heat flow that the cavity insulation does. Often termed "thermal bridges," these sticks have a significantly reduced R-value.
In addition to the sticks are holes. The holes are windows and doors, typically referred to as "fenestration." The fenestration in most cases has much lower insulating value than the center of cavity insulation. For marketing and standardizing purposes, we like to use the higher R-value of the insulation when discussing exterior wall assemblies. Using the higher R-value number, we feel better about our battle with the environment, and we look better. Reality, however, tells a slightly different story.
When we build exterior walls, we have three major contributors to the assembly—insulation (cavity or continuous sheeting), the wood frame, and the windows and doors. These three contributors when considered together make up what we call "whole-wall R-value." The whole-wall R-value is typically significantly less than the standardized value stated as the cavity insulation, mostly due to the significantly lower R-value of the wall frame and the fenestration. When we normalize the R-values of the components, we also have to acknowledge their respective quantities in the wall assembly. Of course, the quantities available for selection are on a very wide spectrum. Although we could write books on this topic, let's boil this down to a clear, simple understanding that we can take away with some confidence.

Framing. Start with the first component of the exterior wall—the wood frame. The wood frame is typically 2-by material showing a 1 1/2-inch face to the exterior. For our discussion, we will call this the "opaque area." Framing has a spectrum of choices to adhere to, such as standard framing, advance framing techniques, and insulated headers (or no headers in non-bearing walls). Walls 1 and 2 (see illustrations, above) show a quick representation of a 16-inch-on-center wall compared with a 24-inch-on-center wall.
I have done numerous framing studies on houses and typically, the delta of opaque area in the walls ranges from about 5% to 12%. Yes, this could be lower or higher based on our level of aggressiveness, but for the sake of discussion, I will use an 8% framing factor to discriminate between a standard frame and an advanced frame. In a typical home, the wood frame comprises an opaque area of about 22%. With advanced framing measures, the opaque area falls to about 14% of the wall assembly. I use R-1.25/inch for R-value of framing lumber. This yields R-4.37 for a 2x4 wall and R-6.88 for a 2x6 wall. In summary, the opaque area makes up 14% to 22% of the wall assembly, yielding an R-value of 4.4 to 6.9 depending on framing thickness.

Cavity insulation, like framing, has options. A 2x4 wall cavity can be insulated from R-13 to roughly R-25. A 2x6 wall can be insulated from R-19 to R-39. Material selection, density, and cavity depth all play a role in the "cavity" R-value of a wall. For the purpose of our discussion, we'll use R-15 for a 2x4 wall, and R-21 for a 2x6 wall. The amount of cavity insulation has a direct association to the decisions of construction of the wood frame. This is simply because where there is no wood frame, there is typically cavity (except at windows and doors). So a decision for aggressive advanced framing techniques will yield a higher cavity percentage. Just like the wood frame, the delta of "cavity" area is 8%. Typically, the cavity area will vary from 63% to 71% of the wall assembly, directly tied to framing decisions.
Windows and doors are the last component of the exterior wall assembly. Not unlike their counterparts, the wood frame and cavity insulation, windows and doors have numerous insulating options, sizes, and performance enhancements, and most importantly, a wide spectrum of "fenestration" percentage. For the sake of our discussion here, we will use a window/door package with a U-value of .30. The U-value is the reciprocal of R-value; therefore, 1/.30 yields an R-value of 3.3. With the amount of glazing varying so widely, I resort to a simple colonial home yielding about 15% of the total wall assembly dedicated to "fenestration."
You can now see that as we construct our wall assemblies that the typically stated "R-value" (the cavity-insulation value) is not nearly the value of the whole-wall R-value, which normalizes the cavity area and cavity-insulation R-value with the areas and R-values of opaque and fenestration. Together, the three of them offer a not-so-staggering R-value. Walls 1, 2, 3, and 4 in the first two illustrations above use typical residential construction materials. The takeaway of note here is how the "stated" R-value (the R-value of the cavity insulation) actually compares with the whole-wall R-value: In all cases, whole-wall R-value (what is actually happening) is considerably less than the stated value.
As noted, you can see a distinct compromise for what we label our wall's R-value and what we are actually constructing. In terms of the 2x4 16-inch-on-center wall, the whole-wall R-value is actually only 48% of the standard labeled value. Increasing the depth of the wall and cavity to 2x6, the whole-wall R-value is 43% of the standard labeled value. Instituting a level of advanced framing to the 2x6 wall yields a whole-wall R-value of 9.6, only 46% of the standard labeled value.
Evaluating Real-World Options
Please understand: I am not advocating for not insulating or saying that insulation is a waste of time or that advanced framing isn't worth it. I am simply trying to share a better understanding of what we as an industry are actually doing. This understanding will assist us in making informed decisions as we move forward in developing solutions to our clients' problems.

In Walls 1, 2, and 3, we see that we didn't achieve even 50% of the standard labeled value. That's not a failure—it's the science of building. The important question we need to consider if we want to improve the science is, How can we create a better wall? Because the wall assembly has three major components—the wood frame, the insulation, and windows and doors—we need to evaluate each component separately.
Framing depth. Let's start with the framing. Specifically, what happens when we increase the framing depth from 2x6 to 2x8 at 24 inches on-center?
As Wall 4 shows the increase in frame depth provides more insulation value in the cavity, but it doesn't change the whole-wall R-value much. The important point to understand here is that even though the cavity insulation R-value increases in a fatter wall, the R-value of the stud is only minimally enhanced, and more importantly, the stud remains a thermal bridge.
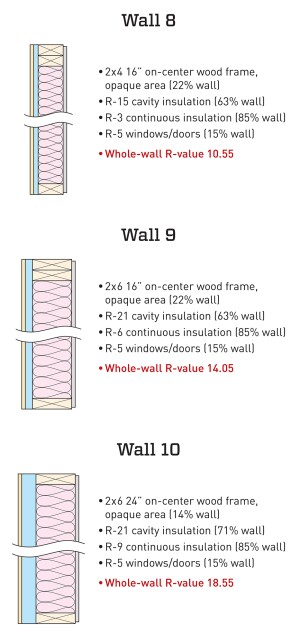
Continuous insulation. What's the next level of improvement? The wood-framed opaque wall areas with cavity insulation areas account for roughly 85% of the wall. If we step outside of the frame to the exterior and add rigid insulation, we not only add R-value, enhancing the cavity insulation, but we also shut down the thermal bridges created by the framing, which greatly enhances the R-values at the opaque areas. Walls 5, 6, and 7, shown in the illustrations above, show what happens to the whole-wall R-value of the first three walls when we add continuous insulation.
By using continuous insulation, we increase the whole-wall R-value. The thicker the continuous, the greater the increase. I am a big advocate for continuous insulation in any climate where we purchase energy to improve our interior environment. Its benefits also extend into realms of durability, health, and comfort. (In this article, we are focusing on energy performance, but it's important that we acknowledge the other critical performance factors that are affected by the energy performance of the wall, and which we can discuss in detail at a later time.) The interesting takeaway here is found when you compare images: Wall 5—a 2x4 wall with R-3 continuous insulation is arguably the same wall as Wall 2—a 2x6 16-inch-on-center wood-framed wall—at least from strictly an R-value perspective. But the science of our walls is not quite complete. Like insulation, windows offer a spectrum of performance. Let's see what happens when we alter the window performance in some of these walls.
Window options. Note that in all instances in Walls 5, 6, and 7, the window and door openings—at 15% of the wall—were the worst performing part of the wall.
Compare those whole-wall R-values to the last three wall examples: Walls 8, 9, and 10 (see illustrations, above). Notice that what we are doing is improving the wall proportionally. By addressing the largest areas of the wall first, we make incremental improvements, and as we do so, the smaller areas (in this case, our window/door area) become more and more important. Addressing the windows and doors once we have addressed the opaque and cavity areas leads to the best wall performance. So we start with insulation—a good thing—and then advanced framing is a preferred option that makes insulation look even better. Continuous insulation will always be a good choice. And better windows make sense, but only after we attack the higher-proportion areas of the wall.
Years ago, I had lunch with one of the best building-science minds in building history. As an aspiring young architect looking for a quick, down-and-dirty answer, I asked him, "What's the best wall I can design/build?" His reply was simple and confident, "Put as much insulation on the outside of the wall as you can afford." That's sound advice. In addition, know that windows, even the best ones you can find, will most likely always be the worst performing part of the wall. But to me, the most important takeaway here is the idea of "proportional development." It doesn't make sense to put a mediocre, R-3 window in a high-performance, R-30 wall. As we, the architects and builders (the professionals), address solutions with our clients, we need to understand that each of the components should be "proportional" to the whole—in this case, "whole-wall R-value." Long live our buildings.
Source: https://www.jlconline.com/how-to/insulation/understanding-r-value_o
0 Response to "Residential Wall With R13 and 5 Continuous"
Post a Comment